Only the best is good enough for the 200-meter-tall building Tornado Tower in Doha, which was the highest building in MENA (Middle East - North Africa) at time of construction in 2008.
The Project is using FlowCon valves and won a price of being the best and highest building in MENA.
The Tornado Tower, also called the QIPCO Tower, is an iconic building in Doha, the capital of Qatar, completed in 2008. The Tornado Tower is a monument for Doha and building technology. With its intelligently networked building systems, the interior of this building sets new standards. The desert metropolis of Doha has got a new 200-meter-high landmark. The tower enhances the skyline with its unique architecture. It has won the price of being the best and tallest building in the Middle East and Africa by the Council for Tall Buildings and Urban Habitat.
At night the high-rise with its state-of-the-art lighting system becomes a shining example of innovative building technology.
Tornado Tower utilizes an efficient striking structural system to house 52 floors of office space in a 200-meter-tall building. In addition, the project aims to minimize effects on the natural environment through proper site utilization, innovative usage of materials, energy reduction, reduced emissions and water consumption. The building demonstrates relevance to the contemporary and future needs of the community in which it is located, and adds economic vitality to its occupants, owner and community.
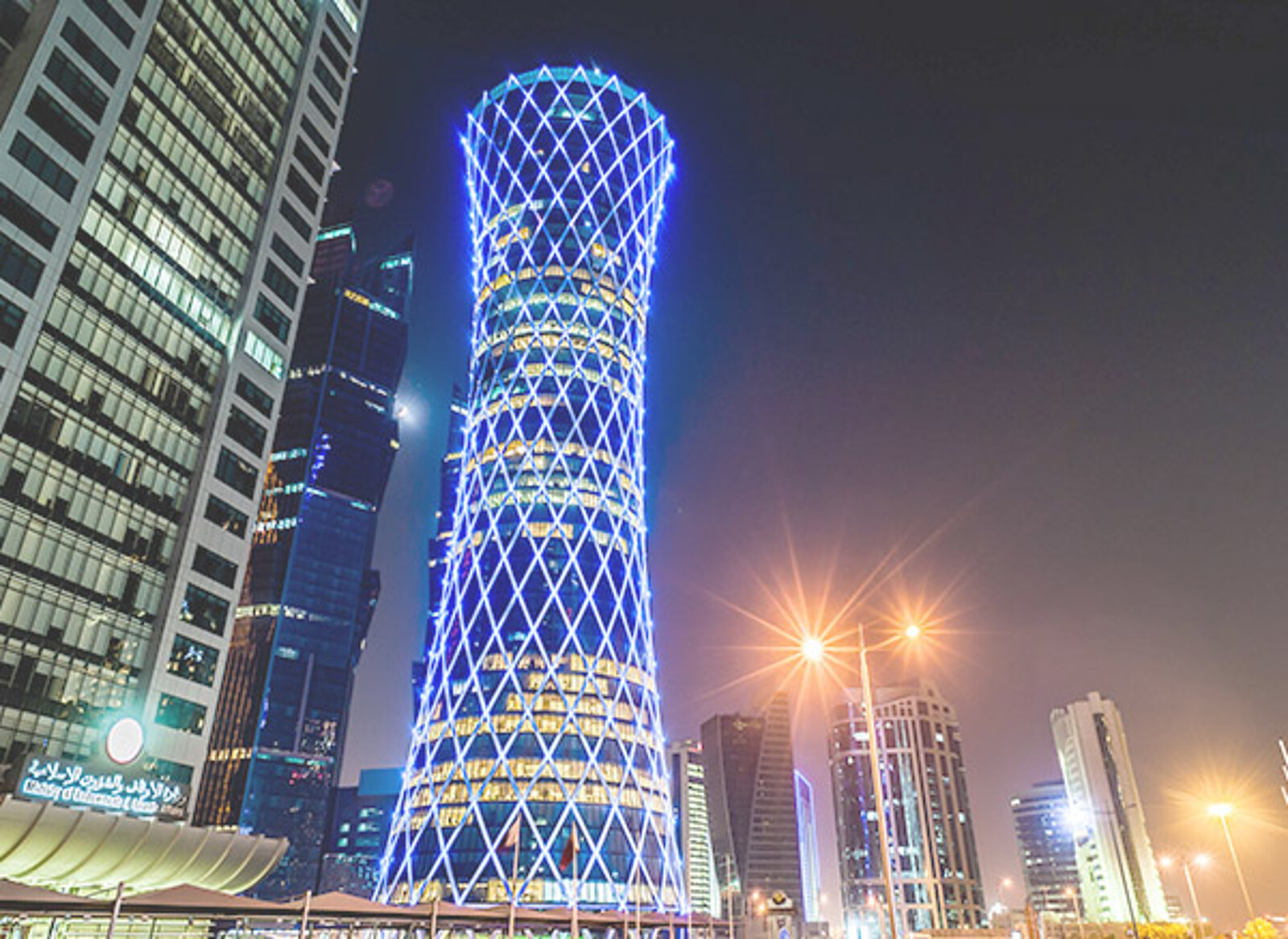
Project Configurations
Contractor: | MIDMAC/Six Construct |
Architect: | CICO (Qatar)/SIAT (Munich) |
Structural Engineer: | CICO/SIAT/Meinhardt Singapore |
Project Name: | Tornado Tower, Doha, Qatar |
Configuration of Building: | AHU´s, FCU’s and Chillers |
Number of Valves: |
1,277 PICV’s for fan coils 28 PICV’s for AHU’s 24 PICV’ for Heat Exchangers 10 Automatic balancing valves for heat exchangers and fresh air handling units 8 Automatic balancing valves for Chillers 4 Automatic balancing valves for cooling towers |
Valve Model: |
FlowCon Green DN15-25 FlowCon SM valves size DN25-DN150 FlowCon Wafers DN200-DN350 |
Type of Job/Application: | New building/cooling |
Date of Installation: | Completion December 2008 |
Total Area above Ground: | 80.000 m² |
Total Area below Ground: | 55.000 m² |
Total Height/Floors: | 200 meters/52 floors |
Cost of the Project: | $200m |
Tornado Tower is located in the thriving West Bay business district of Doha. Its name reflects its architecture – the tower resembles a tornado in the desert. The impressive skyscraper offers 58,000 m² of world-class office space over 52 floors. In addition, it houses shops, restaurants and a health- and fitness center. High-speed elevators running at a speed of approximately 8 m/sec bring users to their desired destination.
The goal was to intelligently integrate all building technology disciplines to make the Tornado Tower a landmark for maximum security, energy efficiency and flexibility while offering the highest level of comfort. The name Tornado was developed by the design team to describe the distinctive, hyperbolic shape of the building. This form is enhanced by a unique lighting system, designed especially for the tower. The kinetic light sculpture, by its movement of light, suggests the torsion of a tornado. The lighting system is programmable and can produce over 35,000 variations of lighting patterns to create a stunning visual effect at night.
To construct a relatively lightweight building, a tubular steel “diagrid” structural external envelope was employed. The diagonal pattern of the skin increases the stiffness of the lateral force-resisting system of the perimeter walls. The concrete core of the building is connected to this perimeter structure with clear spanning steel beams topped with composite slabs creating a flexible, column-free office space at each floor level. All floors are also designed with state-of-the-art raised flooring systems to maximize flexibility for office space planning.
Located on a flat site of 18,500 m² (199,000 sq ft), the building occupies only around 3,000 m² (32,300 sq ft) of this, leaving free space around it to enhance the striking visual appearance of the building’s form and shape. The circular footprint of the building, with a diameter of 60 meters (197 ft) at the ground floor, includes a restaurant, a bank and support facilities.
Sixteen high-speed passenger elevators swiftly serve over 84,000 m² (904,000 sq ft) of office space throughout the building, a first-floor cafeteria and conference rooms and the 27th floor recreation area which includes a gym and a juice bar. The building is including 1,700 car parking spaces housed within three levels of underground basement parking.
Due to the shape of the building, the total lettable office space available on each floor varies from 1,260 to 2,400 m² per floor (13,560 to 25,800 sq ft). This offers high flexibility in both the size of office space available and the specific sub-division layout of office space within those areas. Surrounded by 360-degree view terraces, the topmost three floors of Tornado are dedicated to VIP offices.
The design of the building is an honest one in that the structure is an integral part of the design expression - it is on show with the exposed tubular structural system of the facade clad in part with aluminum composite panels. High performance glass and internal sun shading devices ensure that cooling costs are reduced, and architectural detailing ensures a relatively airtight building, reducing air leakage to a minimum. In addition, rainwater is recycled and used for irrigation purposes. Fire safety measures include dedicated fire lifts and extra stairs. The use of a steel perimeter structure, rather than the more usual concrete structure predominantly utilized in the region, provides much more than a slender structure as it maximizes the uninterrupted panoramic views across the city and beyond.
The building itself makes a positive impact to the whole West Bay area of Doha. As an instantly recognizable focal point it brings context and positional sense to the streetscape with the building situated in a wide, open plaza rather than mounted on a podium. The surrounding areas are left relatively uncluttered with the provision of car parking hidden away below ground, leaving only visitor parking at street level. Detailed traffic impact assessments were carried out to ensure the infrastructure in place was sufficient to cope with the additional vehicular movements anticipated to be generated by the fully occupied building.
Despite the project being a prime example of a fully integrated solution consisting of power distribution, building automation, fire safety and security systems unified in one management station, all involved parties acknowledged the requirement of including a hydraulic specialist as FlowCon International to ensure that the indoor comfort and energy efficiency is as impressive as the architecture. The customized Building Management System (BMS) offers an easy-to-operate graphical user interface to control and monitor all disciplines. Ongoing monitoring and reporting make it possible to increase comfort, reduce energy consumption and operating costs, save resources and minimize CO2 emissions.
State-of-the-art video surveillance equipment, innovative access control systems and an intelligent alarm system ensure the highest level of security from the parking garage under ground and all the way to the roof. Integration makes it possible to detect dangerous situations more quickly and to initiate the required measures, such as notifying the personnel in charge via text message (SMS). In addition, critical areas of the building are identified on alarm pop-ups.
FlowCon International had a very close cooperation with the project, making the right customized valve solution to fulfil the specific needs. The project team had a lot of wishes to make the tower a landmark for maximum security, energy efficiency and flexibility while offering the highest level of comfort. There was no doubt that FlowCon International should be the valve supplier for the project as FlowCon International previously had assisted the consultant and contractor for a smaller building of similar circular design called the Sports City Tower, which was the central building of the Asian Games held in Qatar in 2006.
History of Tornado Tower, Doha, Qatar
History of Tornado Tower The 52-storey tower is now the most recognisable building on the Doha shoreline. This ambitious scheme provides 58,000 m² of office space with 360° panoramic views.
A unitized solution - more than 6,000 Wicona unitised glazed panels in 50 size variations - a different panel size for each floor - allow the curvature of the building to be expressed without the need for curved glass.
The Wicona unitised facade uses 450 tonnes of aluminum and was safely installed across 50 stores using floor cranes. The trapezoidal units, which were assembled and glazed off site, hold 34 mm reflective glass for the vision areas and opaque glazing to conceal the building structure between floors.
The unitised panels also support an external steel ‘lattice’. This outer structure is a key architectural feature and lighting installed at the junction points of the steelwork accentuates the form of the building at night, to spectacular effect.
Wicona unitised solutions are particularly suited to high rise, complex and bespoke facade designs. The panels can accommodate any combination of profiles, external feature caps and glazing, and can include stone cladding; metal, composite or polycarbonate panels; windows, doors and fixed light glazing as well as sun shading and photovoltaic
panels.
Karlheinz Beck, Project Engineer, Wicona:
“In addition to helping to realize the architect’s vision for the building’s unique shape from ground to roof, the unitized approach allowed the full height glazed façade to be installed without scaffolding. It also accommodates high building movement, the high wind loadings that the tower will be subject to and efficient drainage, particularly where the building inclines.”
Building Features
The Tornado Tower is located in the West Bay district of Doha - an almost entirely manmade peninsula. Other features of the building include:
• A helipad on the 51st floor
• 16 high-speed lifts which travel at 2 floors per second
• 1,700 parking spaces over three basement levels
• Gym
• Restaurants and cafes
• Retail outlets
• A complex external Thomas Emde-designed lighting system.
Origin: All products were required to be European/USA origin.
Serviceability: The FlowCon products supplied are modular built and can be disassembled for service without removing the valves from the pipeline. Spare parts can be purchased at and replaced by the local distributor or staff from the FlowCon International office. Finally, all valves are supplied with the unique actuator system allowing the same actuator type to be installed on all FlowCon SM valve sizes. This allowed training of onsite staff possible, minimizing spare parts and uniform the data input and output, which is important considering the complexity of the building management system
Performance: The PICVs installed for the fan coils have ±10% accuracy, 100% authority, 100% stroke at all pre-settings with stem operation of the modulating functionality as this valve design was optimal for the customer selection criteria regarding product flexibility, installation flow, initial cost and operations requirements. The PICVs installed for the air handling units and heat exchangers have an accuracy of ±5% and operates over a 2,160° rotation angle, have feedback option to BMS and hold 100% authority at all times making it the most accurate PICV in the world. Besides the PICVs, a variety of dynamic balancing valves holding ±5% accuracy was installed in heat exchanges, chillers and cooling towers.
The valve configuration supplied to the project ensures very accurate control of the HVAC system at all load conditions and operation sequences. With the high accuracy, 100% authority and 100% stroke the ΔT is optimized in the system. Besides the optimized ΔT, the valves installed have a low pressure drop compared to a traditional DRV and 2-way control valve configuration. The increase in ΔT and reduced pump head are estimated to have saved more than 50% of the energy consumption versus traditional DRV with 2-way control valves and constant speed pumps.
Reliability: The FlowCon SM valve has been installed in buildings globally for more than 10 years at the time of order, making it the most well-proven PICV valve in the industry. Based on their previous experiences the construction team felt “in good hands” using the products of FlowCon.
Monitoring: The FlowCon SM valves installed features a feedback function, which will allow the valve to perform self-diagnostic. In case of any issues, the valve can request service through its feature, before any effect is noticed and reported.
More Information
Latest FlowCon Projects
See all projects
New office for Yandex, Armenia
IT specialists gathered under one roof and FlowCon helps to provide optimal working environment with FlowCon Green PICVs
Expansion of Medial Center in Yerevan, Armenia
Vardanants offers high-quality medical services for all
Umm al Seneem Park, Doha, Qatar
New recreational facilities including opening of the world's longest air-conditioned outdoor walking track open the possibility of a healthier…
Netflix Film and Series production on new Sound Stages in New Mexico, USA
The sound stages will secure creating and capturing of sound in high quality. And FlowCon and Griswold HVAC valves will secure the correct indoor…
Upgraded HVAC system at the Radisson Blu Hotel, Yerevan, Armenia
From static to dynamic balancing – from internal to external adjustability – easy exchange with FlowCon ABVs
World’s largest Duty-Free Mall on Hainan Island, China
800 well-known international and domestic brands under one roof, and indoor climate is controlled by FlowCon valves