Controlling ΔT with Traditional 2-way Control Valves
versus Pressure Independent Control Valves
By Torben W. Ibsen, CEO, M.Sc. (Mech.Eng.), FlowCon International ApS, Denmark
Original 10.2009 - Republished 03.2023
The object of this topic letter is to explain how a pressure independent control valve can provide 100% authority and thereby increase the accuracy of the ΔT control compared with a traditional 2-way control valve.
ΔT Control with Traditional 2-way Control Valves
A traditional 2-way control valve is operating 100% on pressure drop. Upon closing, the 2-way control valve will increase the pressure drop in the circuit and thereby reduce the flow rate and vice versa when opening. As the flow rate is decreasing, the other components in the circuit such as balancing valve, coil and pipe work will experience a lower flow and thereby a lower pressure loss.
It is known that the flow through each unit in the system - in this case balancing valve, thermal unit, and pipe work - is defined as:

As the above-mentioned units all have constant areas, the following will apply to these:

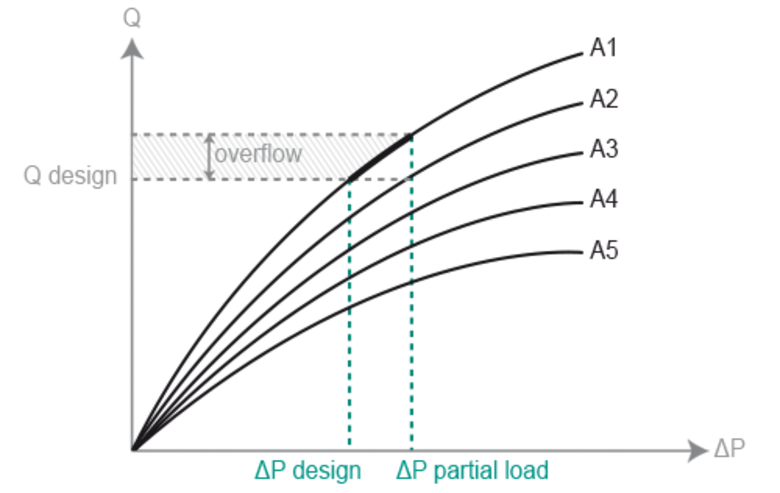
Once the pressure drop is increased through the control valve - by this closing - the ΔP across the remaining loop will be reduced, for which the control valve will further have to compensate by additionally closing. Flow-curve A1 (in figure 1) will move from ΔP design to ΔP partial load, resulting in an overflow if the control valve is fully open. If the control valve is partly open, it will, in order just to maintain a constant flow and to compensate for the pressure fluctuations, have to move from flow-curve A1 to flow-curve A2. The formula is:

and it will have to close even more to reduce the flow rate.
Read more
As it can be seen from above function, the pressure drop of the balancing valve, thermal unit and piping has great impact on the performance of the traditional 2-way control valve as it is pressure dependent.
Based to the pressure dependent function, fluctuating ΔP will lead to fluctuating Q, which again leads to fluctuating ΔT, as per below figure 2.
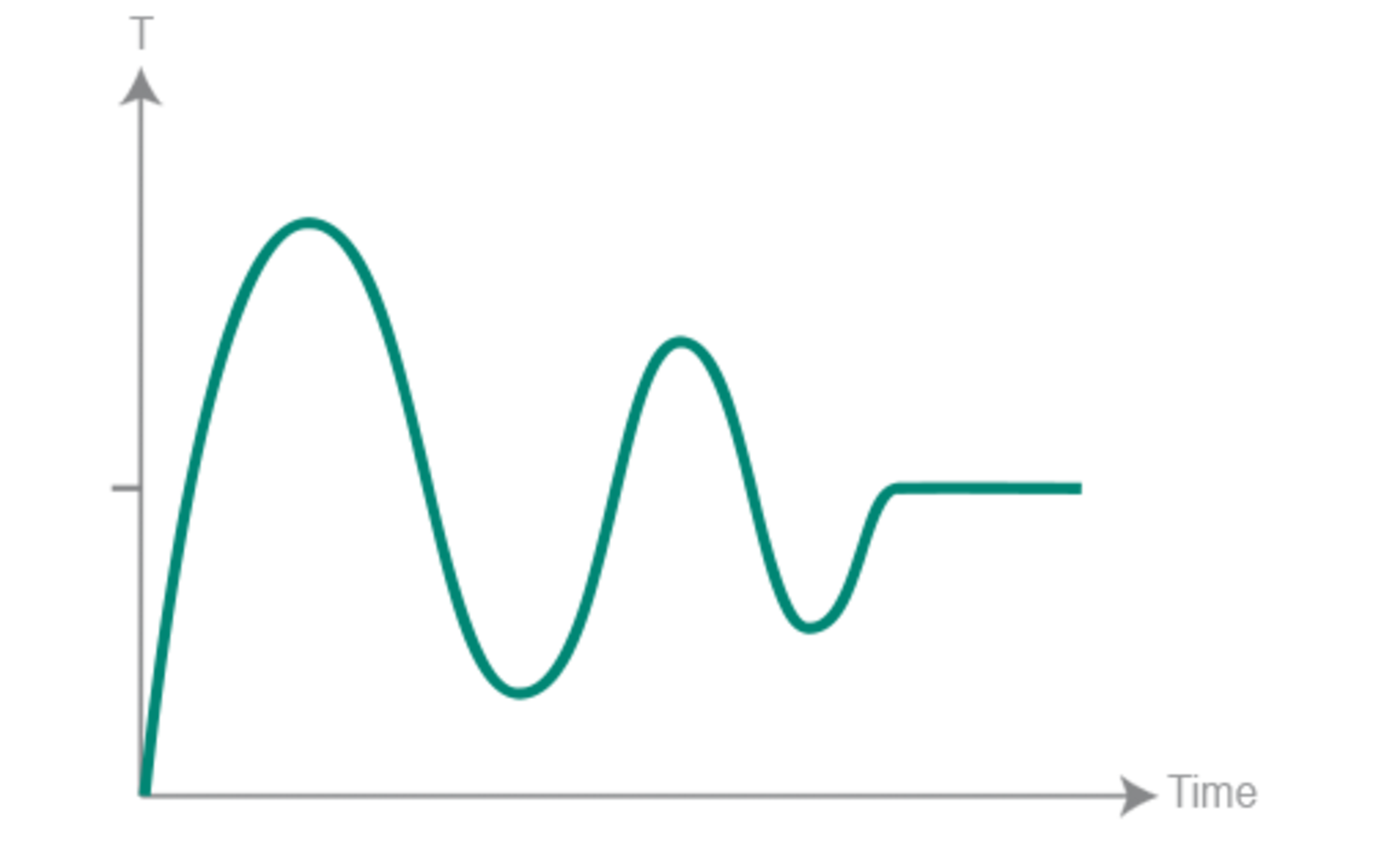
The interaction between the installed units is measured in control valve authority. This is to ensure the proper sizing of the 2-way control valve -or more correctly resistance through the 2-waycontrol valve - and thereby ensure that the 2-waycontrol valve has authority to control the flow rate.The authority identifies exactly how much the 2-way control valve will have to move to compensatefor the other units in the system.
The mathematical form to calculate the authority (Au) of the 2-way control valve is:

As the pipe pressure loss traditionally is low compared to the pressure loss of the other components, this is often neglected, but in reality, it will in fact contribute slightly towards worse authority then the commonly calculated value.
A normally accepted authority is approximately 50%, which indicates the minimum pressure drop accepted in the 2-way control valve to be:

which often amount to a fairly large pressure drop across the 2-way control valve, which again will lead to extensive energy consumption.
Lower authority than 50% indicates that the 2-way control valve will allow substantially more water through the valve than the control signal entitles, providing extensive energy consumption and worse comfort.
If flow rates in a system with 50% authority is examined at 100% and 50% load respectively, the above authority will translate into the graphs illustrated in figure 3.
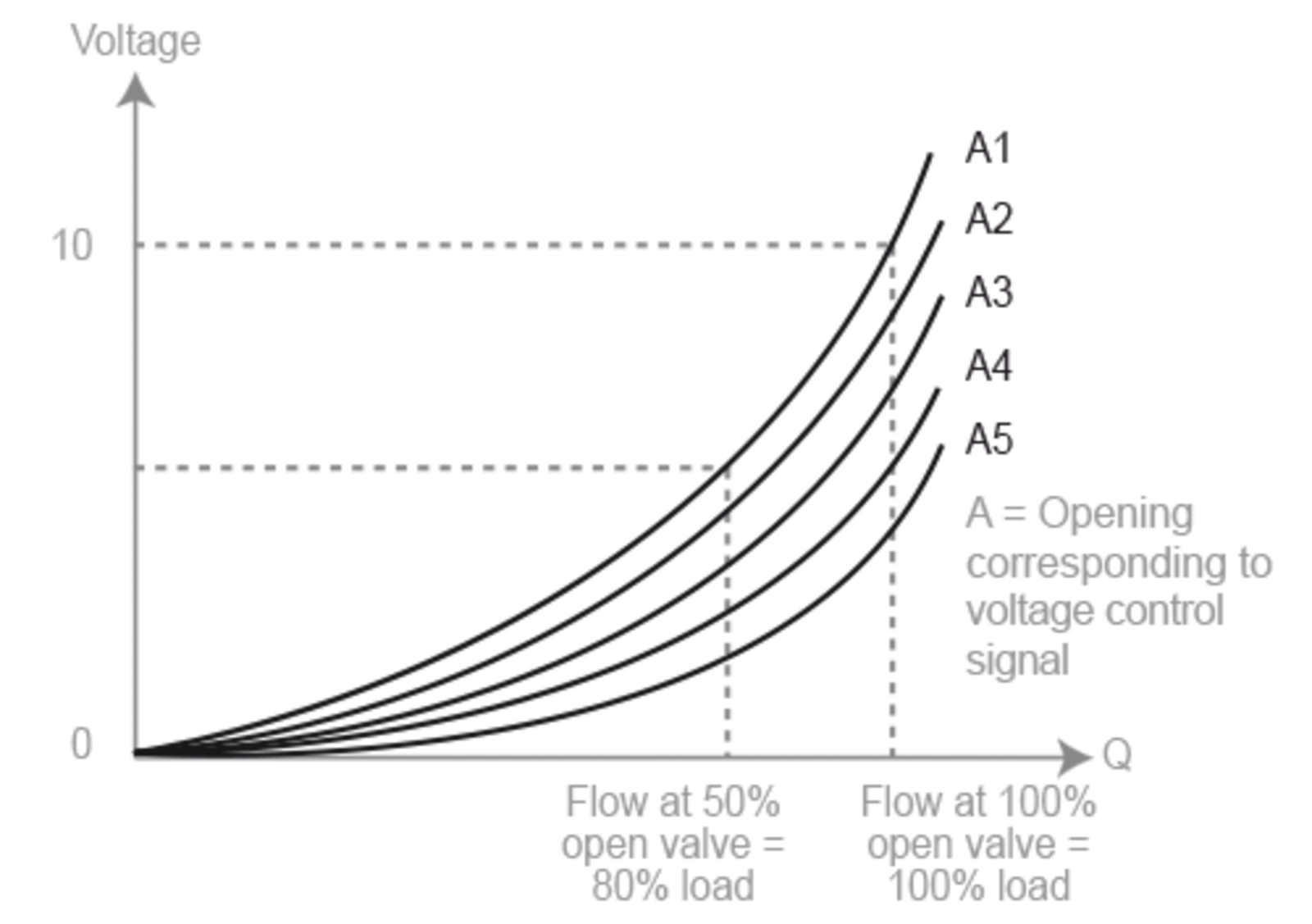
As it can be seen from figure 3 above, the flow does not equal the control signal. This is due to the fact that 100% authority cannot be obtained if the control and balancing valves are separate. Further, it must be noted that to maintain a certain ΔT, a certain flow rate is requested, but due to the fact that substantially more water (80% instead of the needed 50%) is received, this results in what is commonly known as the “low ΔT syndrome”.
This is unavoidable and therefore extremely common when using traditional 2-way control valves in chiller systems. Sometimes, the problems are hidden by unnecessary lowering of the chilled water supply temperature or raising of the air temperature in the coils - both solutions requiring additional energy and “balancing”.
ΔT Control with Pressure Independent Control Valves
A pressure independent control valve, PICV, is characterized by being a combined pressure controlling valve and a traditional 2-way control valve in terms of function. By applying the pressure controlling function to the control valve, the valve will work under the below conditions:

By making the valve pressure independent, each position of the control valve will define a corresponding flow rate. This is illustrated in figure 4.
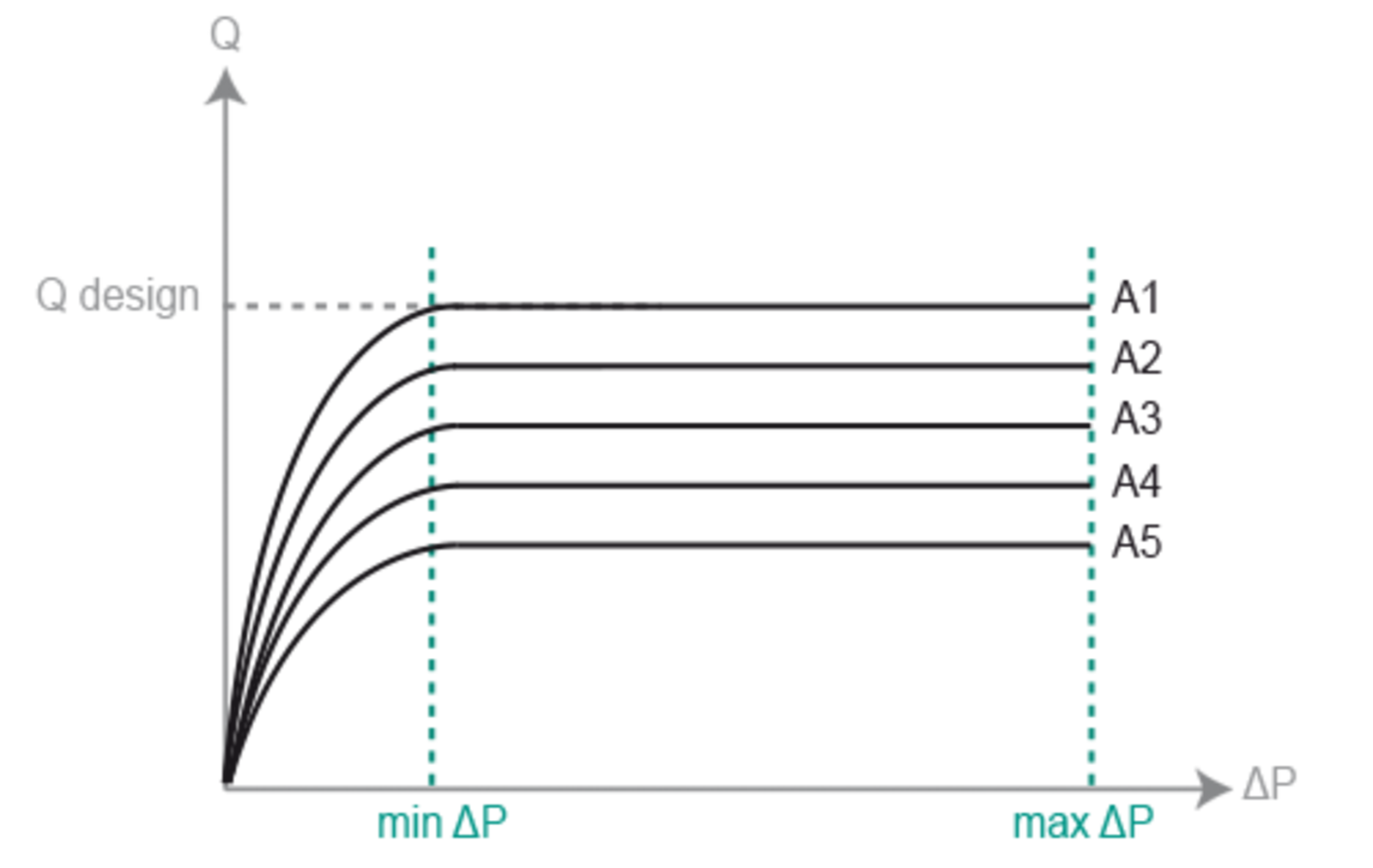
It can be seen from this graph in figure 4, that a change in the pressure is affecting neither the performance nor the flow rate in a pressure independent control valve, PICV. As there is no relation between the pressure drop and flow rate once within the design pressure range, pressure calculations related to the authority are obsolete. As the pressure independent control valve’s opening is the only flow-defining part in the circuit - due to the pressure independent function - this is alone deciding the flow rate, equaling 100% authority.
If flow rates in a system with 100% authority is to be examined at 100% and 50% load respectively, the above authority will translate into the graph illustrated in figure 5.
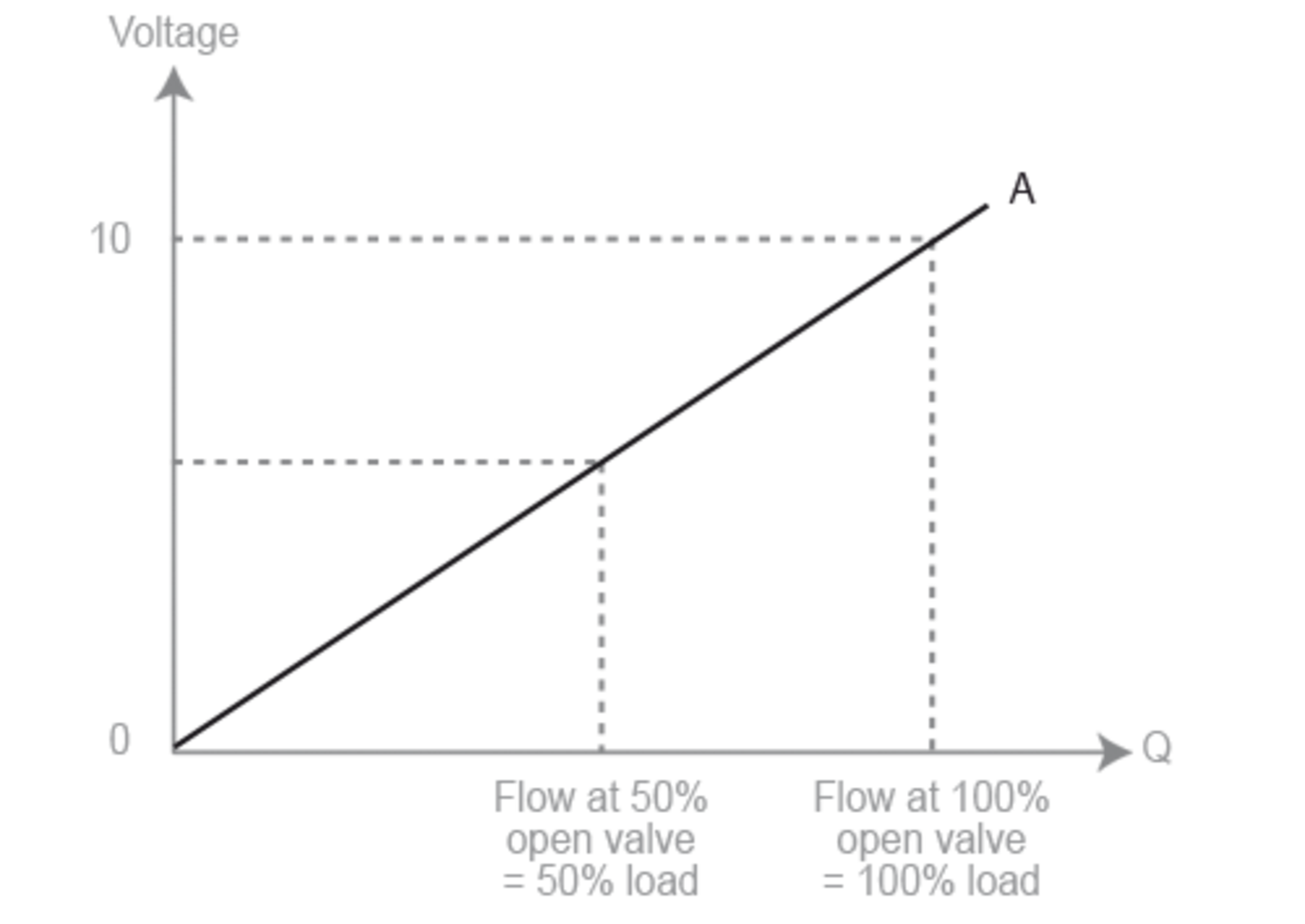
As it can be seen in figure 5, the flow does equal the control signal. This is due to the fact that 100% authority is achieved by building the control valve and balancing valve together.
As can also be seen in figure 5, the control signal is requesting a certain flow rate to maintain a certain ΔT and is actually receiving this flow, unlike the separate conventional solution. Due to the pressure independent function, ΔP remains constant leading to constant Q, which again leads to constant ΔT as illustrated in figure 6. By accurately controlling the flow rate, and compensating for pressure fluctuations, the “low ΔT syndrome” can effectively be avoided.
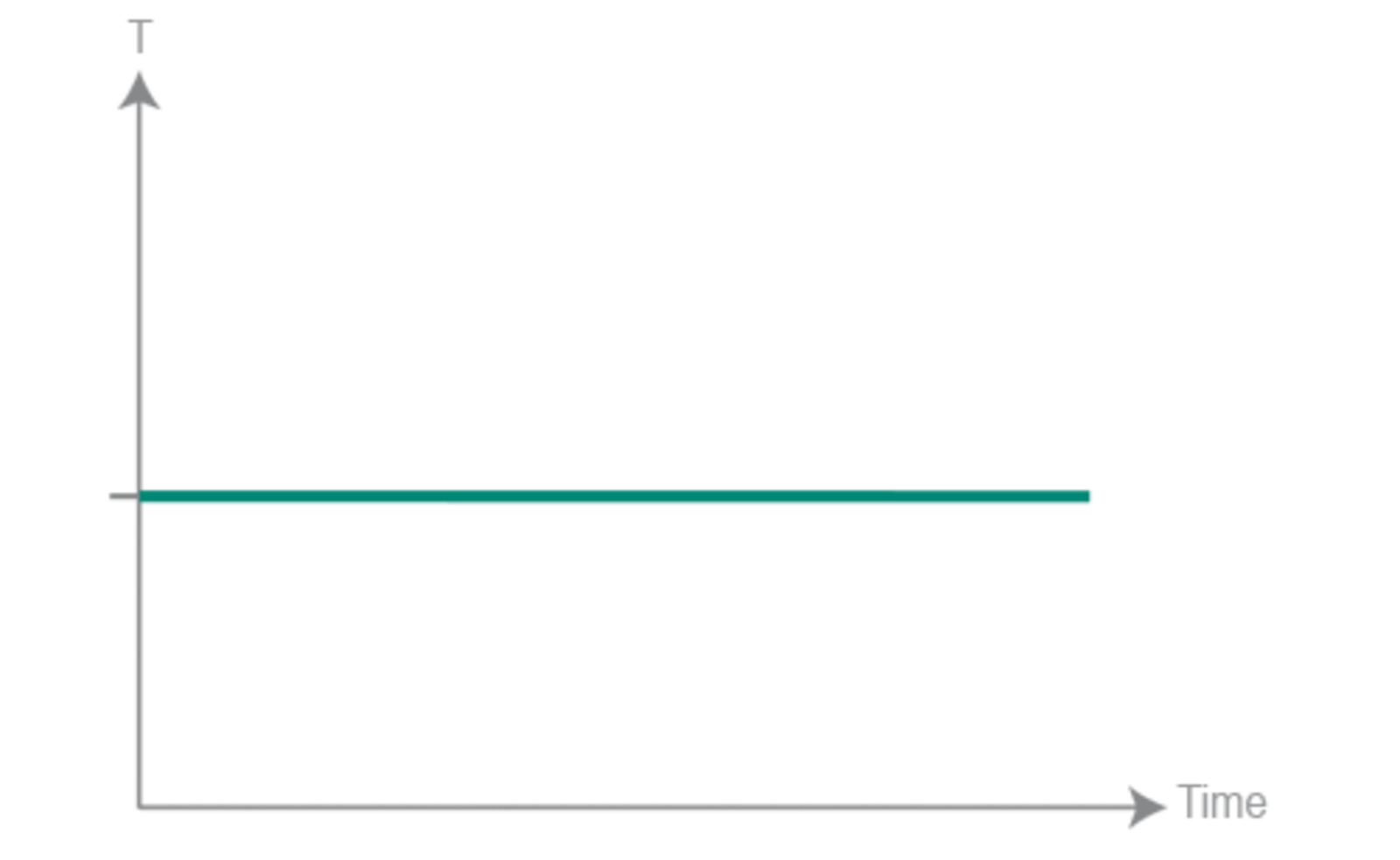
As there is less pressure drop required in a pressure independent control valve, PICV, this technology will additionally allow less pressure drop across the unit and insure better energy consumption.
100% authority indicates that the pressure independent control valve, PICV, will allow exactly the amount of water through the valve as the control signal entitles, allowing optimal energy control and comfort.
Conclusion
Traditional 2-way control valves are responding to pressure drop and are therefore affected by other components in the system, which makes authority calculation necessary. The correct way of calculating the authority is:

Standard accepted authority is ~50%, which indicates the minimum pressure drop accepted in the 2-way control valve to be:

This often amounts to a fairly large pressure drop across the 2-way control valve, which again will lead to extensive energy consumption. Further, even lower authority indicates that the 2-way control valve will allow substantially more water through the valve than the control signal entitles, providing still higher energy consumption, low ΔT and poor indoor comfort.
Due to the authority, it is difficult or impossible to achieve the exact temperature required without further balancing the system and the system is therefore likely to suffer from “low ΔT syndrome”.
Pressure independent control valves, PICVs, are - given by name - pressure independent and therefore not affected by other components in the circuit as long as the pressure drop of the valve is within the design pressure range. As the pressure drop in other circuit-components will not affect the flow rate, these are not to be considered when looking at the pressure independent control valve. Such a valve will therefore maintain 100% authority at all times, as the differential pressure controlling device is compensating for any system pressure changes.
As less pressure drop is required in a pressure independent control valve, PICV, this technology will allow less pressure drop across the unit and ensure better energy consumption.
100% authority indicates that the pressure independent control valve, PICV, will allow exactly the amount of water through the valve as the control signal entitles. This again allows for optimal energy control, improved ΔT control and better comfort. And by accurately controlling the flow rate, the “low ΔT syndrome” can effectively be avoided.
Download Article
Latest FlowCon Articles
See all
Importance of Control Curves in PICVs
Equal percentage control vs. linear control – which is better when and why?
Rangeability and Turn Down Ratio - Update
Definition and use of Rangebility, Resolution and Turn Down Ratio in FlowCon PICVs
Leakage Classification IEC60534-4 - Update
Article is updated to include FlowCon Essentia. All actuated FlowCon valves are classified according to Int. Standard IEC60534-4, Class IV and V