PICV Actuator Gear Material - Metal vs. Composite
By Torben W. Ibsen, President, M.Sc. (Mech.Eng.), FlowCon International ApS, Denmark - 12.2020
This Topic Letter’s focus is on key parameters used for gear material selection in the rotating FlowCon SM actuators and the linear FlowCon FN/FH actuators.
Gear Material
For any gears there is a wide range of various materials are available such as steel, cast irons, nonferrous alloys, various plastics, composites, and synthetic material. Hence, it is important to under-stand the characteristics - including pros and cons - of either solution to ensure selecting the proper material for the specific application. Some gear con-structions will be applicable for certain applications, whereas different gear constructions will be correct for other applications.
Hard-anodized aluminum or steel are in general having their advantage in the durability of the materials, which theoretically should increase the lifetime. This is however not in reality the full truth, as it is extremely challenging to maintain the gears lubricated throughout the actuator’s full lifetime. Once the lubrication wears off, the gears will become increasingly noisy and actuator torque will lessen.
In worst case scenario the metal gear parts will jam up over time, particularly in humid condi-tions. Risk of gear jamming is furthermore related to gear tolerance - the more accurate the gears are, the less wear and tear is seen over time and conse-quently reduced risk of gears jamming. Hence, steel gears are generally recommendable in high torque, high temperature (+180°C) conditions with slow moving operation and low noise sensitivity.
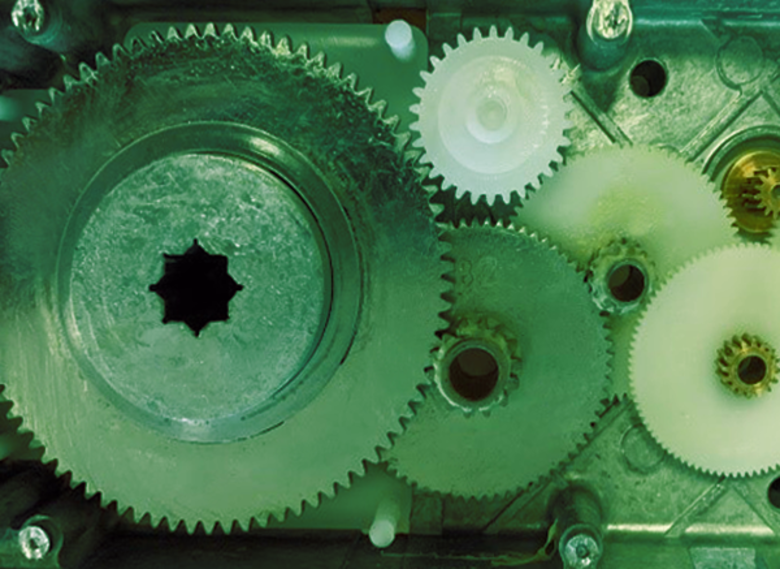
A variety of composite material was introduced in the 60’ies intended for space shuttles and space industries in general. One of these materials was DuPont’s Delrin acetal homopolymer, which was designed to act as a bridge between plastics and
metals focusing on high tensity strength, excellent fatigue endurance, natural lubrication and excellent machineability for better gear accuracy. The product was further developed into the Delrin 150 in the 90’ies, which is the time (1998) when the composite material was introduced in FlowCon SM rotating actuator gears and is still in use today...…
Read more
The SM actuator gear is essentially consisting of a mixture of metal and Delrin 150 gears, see illustration 1 below.

FlowCon SM Actuator Gears
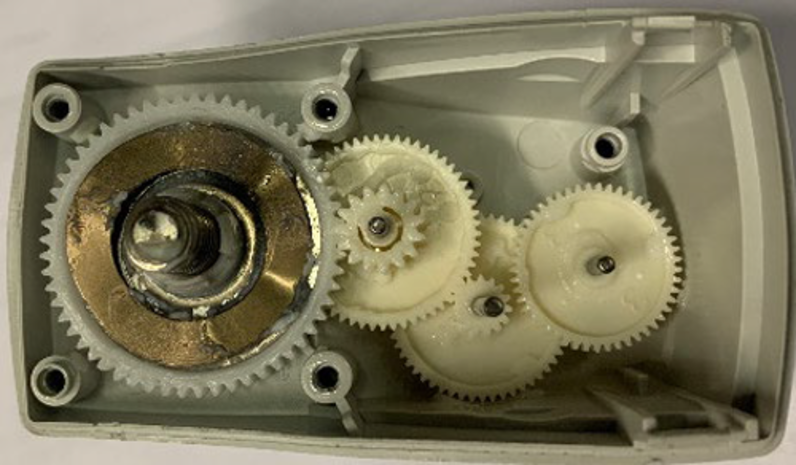
FlowCon FN/FH Actuator Gears
As it can be seen in illustration 1, the actuator gear is designed to each of the used materials strengths. Delrin 150 is used for the smaller gears with smaller load, higher speed, and accuracy demand, whereas metal is used for the larger slower gears with higher loads.
For the stroke actuators FlowCon FN/FH, Pocan BF 4225 is used. Pocan BF 4225 holds an excellent dimensional accuracy and stability, while having excellent slip properties and good strength and hardness making it ideal for smaller actuator gears. In addition to the mechanical properties, the material is flame retardant making it UL certified for gear applications. As seen in illustration 2 no metal gears are included in these actuator types.
The main purpose of the gears in various mechanical application is transmission of toque from one point to another. In FlowCon’s case, it is trans-mission from the motor to the valve spindle.
Application Temperature
Metallic gear actuators are recommended for high temperature applications, which are generally above 180°C. For the lower temperature applications (below 180°C), synthetic material is preferred due to various features and advantages listed below. Recommended FlowCon actuators for FlowCon PICVs are intended to operate within the maximum ambient temperature of 50°C, which is significantly below the mechanical properties of the used composites being up to 150°C.
Gear Friction
Friction between rotating gears will determine gear life, motor performance and temperature increase inside the actuator. Hence low friction is preferred.
Compared to metallic gears, synthetic material gears have minor friction and accordingly emit very little heat. Therefore, it is preferred to have synthetic gear material, if possible.
Cooling and Lubrication
One of the major issues with metallic gears (rotating at high speed) is that those would require lubrication to reduce friction between the gear teeth which ultimately will increase motor size and heat generation. If extremely high temperatures are gene-rated between the gears, it can lead to damaged gears as well as malfunction of other components surrounding them, including the motor, when within the same enclosure. Lubricants may significantly reduce the friction between the surfaces of rotating gear parts, and therefore increase the energy efficiency withing the actuator. Lubricants may also reduce the likelihood of other types of gear failures, such as surface pitting and wear. A good gear lubricant can improve the overall HVAC system stability and increase gear train lifetime. Liquid lubricants, like oil, may also effectively act as coolant, which becomes important, when the performance of components in electro-mechanical actuators degrades as temperature in-creases. Grease is an appropriate lubricant for light load applications.
Thermal conductivity is the essential parameter here. It is for surface hardened steel is 44.5 W/(MK), whereas the same for synthetic material is only 0.299-0.53 W/(MK). Hence, it is both in theory and in practice apparent that synthetic material generates very little heat during operation. Moreover, the material is self-lubricating, which obviously excludes the necessity of separate lubrication to avoid the issues see with metallic gears.
Wear and Tear
Wear and tear are quite high in metallic gear ma-terial due to high friction and high temperature. These factors lead to lower life, increased lubrication requirement and potential failure of actuator.
Noise
Noise is one of the most important criteria when selecting the proper gear material, as noise gene-ration would determine the suitability of the actuator for the specific application. Since PICVs are used mainly for human comfort i.e. in chilled / hot water air-conditioning applications, the valves are mounted in close vicinity of people and therefore also close to catalysts sensitive to high noise levels. It has been proven in various studies that a high noise level lead to low performance and lower comfort level, despite good air-conditioning and room temperature comfort. Hence, FlowCon pays special attention to the noise factor and ensures that actuators are designed for low noise application.
As per actuator gear design, smaller gears are moving at high speed. This is not achievable with metallic gear type actuators and these would defi-nitely have significantly higher noise levels. That - along with the temperature ratings and additional lubrication requirements - is the main reason for actuators with metallic gear is be recommended for industrial applications only.
Impact Dampening Ability
The gear material is selected to reduce the impact from the motor to the valve and also in-between the gears, which is extremely essential for the smooth operation of the valve and the HVAC system. Hence, the actuators are provided with small gears in synthetic material when mounted close to the motor.
Complex Geometries
Small gears for both threaded- and flanged valve actuators are often made of composites, as they generally are rotating faster. Teeth are furthermore finer on the smaller gears, which favors injection molding as the manufacturing method due to smaller material shrinkage and more accurate geometries. Larger gears on SM actuators are however in metal, as these must hold larger teeth, handle higher torque, and will be used in slower movement.
Conclusion
Choosing the ideal gear material is important. Having mentioned various aspects concerning the material of gears for PICV actuators, it may notice that FlowCon uses a mix of synthetic and metallic gears for the SM actuators. This is due to each gear material’s merits and benefits. The smaller gears at the motor end are fast moving, which requires material procuring less noise, low friction, and self-lubrication. Consequently, these are selected in composite material. Larger gears at the valve/ spindle end are of metallic construction due to high torque requirements and slower movement.
For the FN/FH actuators, FlowCon merely uses composite gears for the same reasons, i.e. direct motor location resulting in fast movement requiring less noise, low friction, and self-lubrication.
FlowCon hopes that this Topic Letter has given insight to the topic. Please feel free to contact FlowCon for further assistance or any clarification.
Download Article
Latest FlowCon Articles
See all
Importance of Control Curves in PICVs
Equal percentage control vs. linear control – which is better when and why?
Rangeability and Turn Down Ratio - Update
Definition and use of Rangebility, Resolution and Turn Down Ratio in FlowCon PICVs
Leakage Classification IEC60534-4 - Update
Article is updated to include FlowCon Essentia. All actuated FlowCon valves are classified according to Int. Standard IEC60534-4, Class IV and V